Why Compression Moulding are Used in the Process for SMC Composites?
Join Date: 2023-04-06
SMC (Sheet Molding Compound) compression moulding is a manufacturing process used to produce composite materials. It involves compressing a pre-prepared mixture of chopped fibers, typically glass or carbon, and a thermosetting resin, such as polyester or epoxy, between two heated moulds to create a finished part.
-
1.Preparing the SMC: Sheet Molding Compound is typically produced by mixing chopped fibers (such as glass or carbon) with a thermosetting resin, along with other additives such as fillers, pigments, and release agents. The mixture is typically in the form of a sheet or a mat.
-
2.Placing the SMC in the mould: The SMC sheet is placed in the mould, which is usually made of steel and consists of two halves that can be opened and closed. The mould is typically coated with a release agent to prevent the SMC from sticking to the mould during the curing process.
-
3.Closing the mould: The two halves of the mould are closed, and pressure is applied to compress the SMC sheet. The pressure is typically applied hydraulically and can range from several hundred to several thousand pounds per square inch (psi), depending on the specific material and part requirements.
-
4.Heating and curing: The closed mould, with the compressed SMC, is heated to a specific temperature, typically in the range of 120 to 180 degrees Celsius (250 to 356 degrees Fahrenheit), depending on the resin used. The heat causes the thermosetting resin to cure and harden, forming a solid composite part.
-
5.Cooling and demoulding: After the curing process is complete, the mould is cooled, and the pressure is released. The mould is then opened, and the finished SMC part is demoulded. The part may require additional trimming, drilling, or other post-processing operations to achieve the desired final shape and finish.
The primary reason is that it allows for precise control over the shaping and curing of the composite material, resulting in
high-quality finished parts with desirable properties. The compression process involves applying pressure to the SMC sheet during the moulding process, which offers several advantages:
-
• Consistent and uniform pressure: Compression moulding ensures that pressure is evenly applied to the entire surface of the SMC sheet, resulting in consistent and uniform distribution of the resin and fibers. This helps to achieve consistent part dimensions, thickness, and mechanical properties throughout the finished part.
-
• Efficient resin impregnation: The applied pressure during compression helps the resin to impregnate the fibers in the SMC sheet thoroughly, ensuring good wet-out and optimal resin-to-fiber ratio. This results in a composite material with uniform mechanical properties and improved strength and stiffness characteristics.
-
• Reduced voids and porosity: Compression moulding minimizes the occurrence of voids or porosity in the finished part. The pressure applied during compression helps to eliminate air or gas bubbles that may be trapped in the SMC sheet, resulting in a denser, higher-quality composite part with reduced defects.
-
• Improved part consolidation: Compression moulding allows for the consolidation of multiple layers or sections of SMC sheets into a single part during the moulding process. This can result in parts with integrated features, such as ribs, bosses, and reinforcements, which can improve part strength and reduce the need for additional assembly steps.
-
• Control over part thickness: Compression moulding allows for precise control over the thickness of the finished part by adjusting the gap between the mould halves and controlling the amount of SMC material used. This enables the production of parts with consistent thickness and dimensional accuracy.
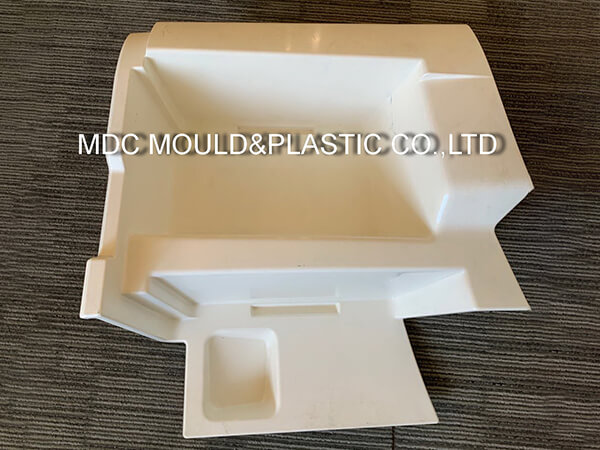
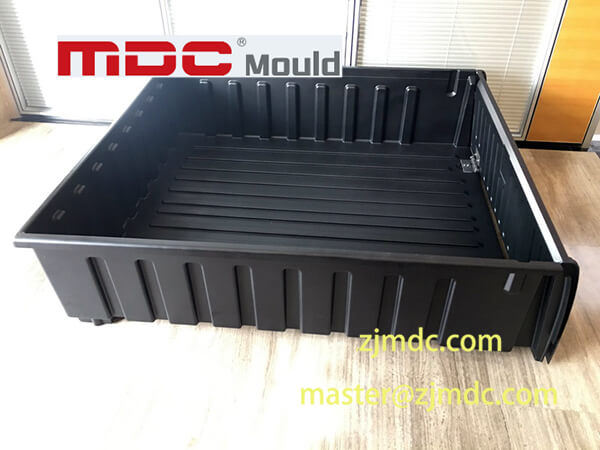
Overall, compression moulding is a well-established and widely used process for SMC composites due to its ability to produce high-quality, complex, and consolidated parts with excellent mechanical properties. SMC compression moulding is commonly used in the automotive, aerospace, and construction industries, among others, to produce lightweight, high-strength composite parts with complex shapes and excellent mechanical properties. It offers advantages such as high production efficiency, excellent part reproducibility, and the ability to produce large, integrated parts in a single moulding process.
As a professional and world-famous mold manufacturer, MDC Mould specialize in SMC mold, compression mold. If you have any need, we will provide the best solution. Please feel free to ask us.